This year
91 companies submitted a total of
184 hazard controls for the
Hazard Control Recognition Awards. Out of those submissions, five of those hazard controls were selected to receive the President's Award. These submissions were selected by the IISC Board of Directors President, President-Elect, and Past President for their outstanding contributions with controlling hazards and were presented with their award at the Professional Development Conference & Expo Awards Luncheon on Friday, April 12, 2019 in Dubuque, Iowa.
Congratulations to these companies for being awarded the President's Award!
D.C. Taylor Co. - Cedar Rapids, IA
Competent Person Enhancement and Rescue Capabilities - In reviewing our Fall Protection Plans and Job Hazard Analysis for our industrial roofing jobs, we identified that we did not have the capabilities defined for fall rescue beyond calling 911. We updated our fall protection plans to include the various options we have for fall rescue and listed them for Supervisor referral on the site. In the winter of 2018, we trained and certified over 60 Project Supervisors and Lead Men in Competent Person Personal Fall Arrest Systems and trained each one in fall rescue with the rescue pole retriever system and rescue ladder. Through this process, we began requiring our Supervisors and crew onsite to identify specific rescue options including rescue pole with retrieval rope; cable retrieval from our AES Raptors; or rescue ladder deployment with a separate anchor point, ensuring that the rescuer is securely anchored with their own personal fall arrest harness, lanyard, and anchor point. Other options are available from an aerial work platform or extension ladder from underneath. The Job Hazard Analysis must specify these options and the crew must acknowledge the rescue plan. We also mandated self rescue equipment on every employee's harness in the form of Trauma Straps. Every new hire goes through the Personal Fall Arrest Systems Authorized User Training, which includes being "hung" by a forklift with their harness and coached on how to deploy and use their trauma straps to prevent Traumatic Orthostatic Hypotension. The training is an eye-opening experience for new hires and they review this monthly with their Project Supervisors.
ATEK Metal Technologies - New Hampton, IA
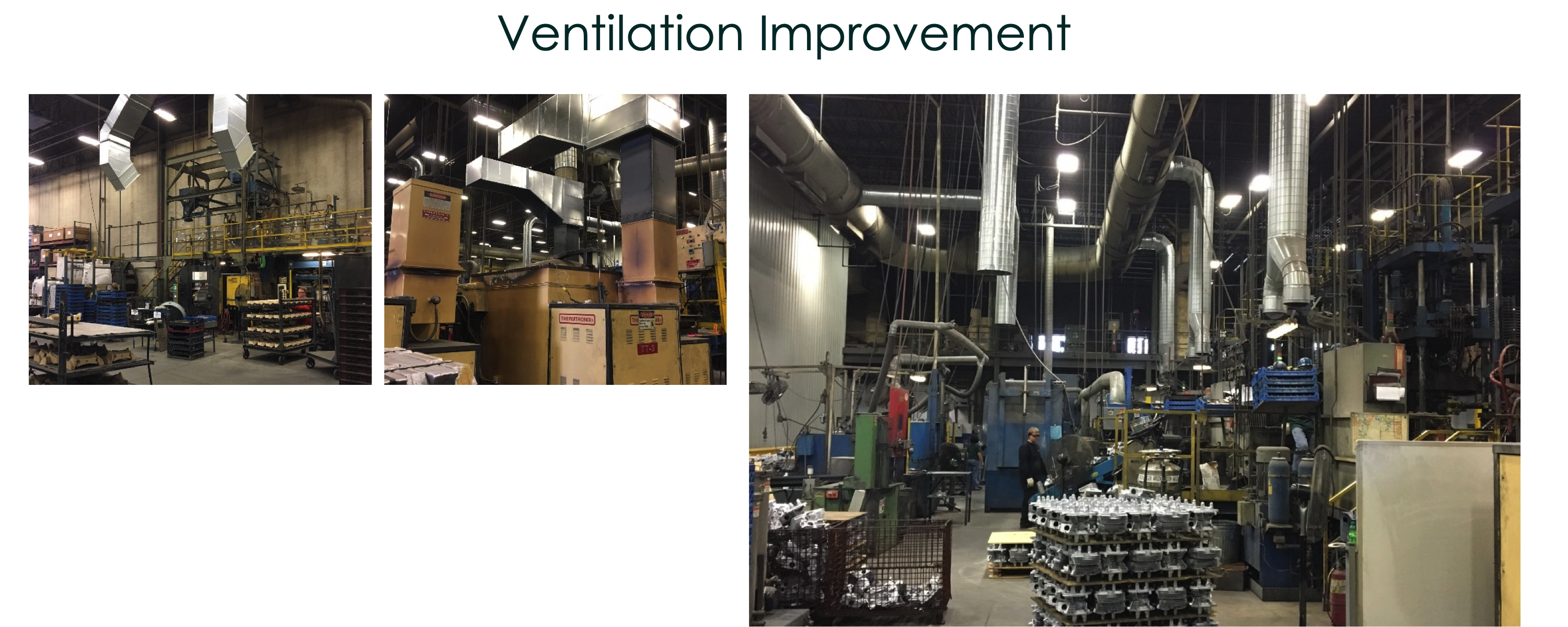
Ventilation Improvement - As a foundry, we experienced several heat related illnesses in summer months. We invested in a large ventilation improvement project which: Improved comfort and air quality in the foundry, reduced heat related illnesses to zero illnesses, and generated very positive feedback and appreciation from employees.
Stellar Industries - Garner, IA
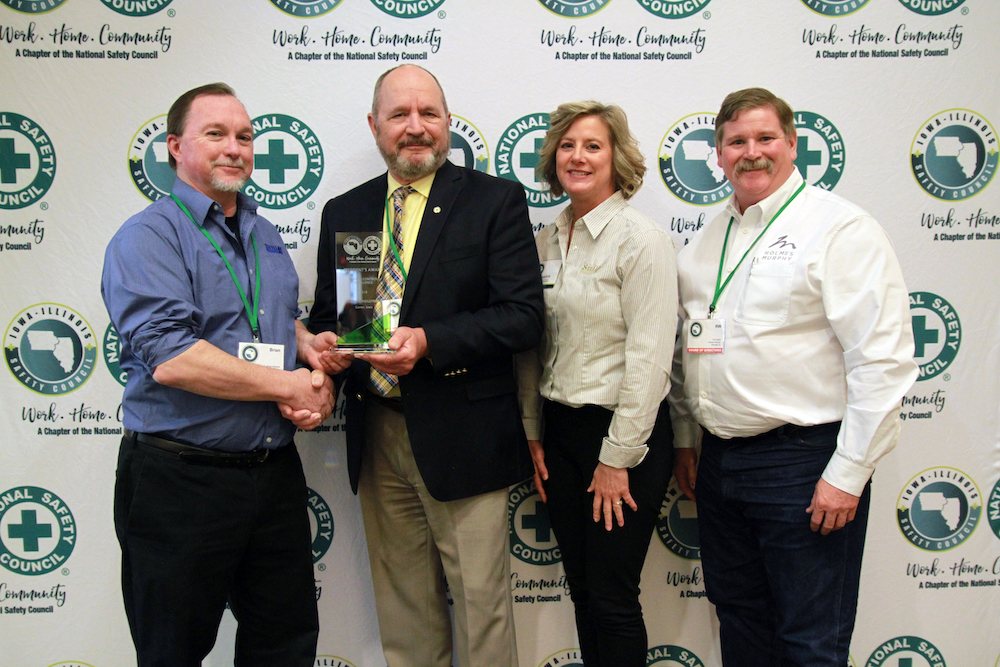
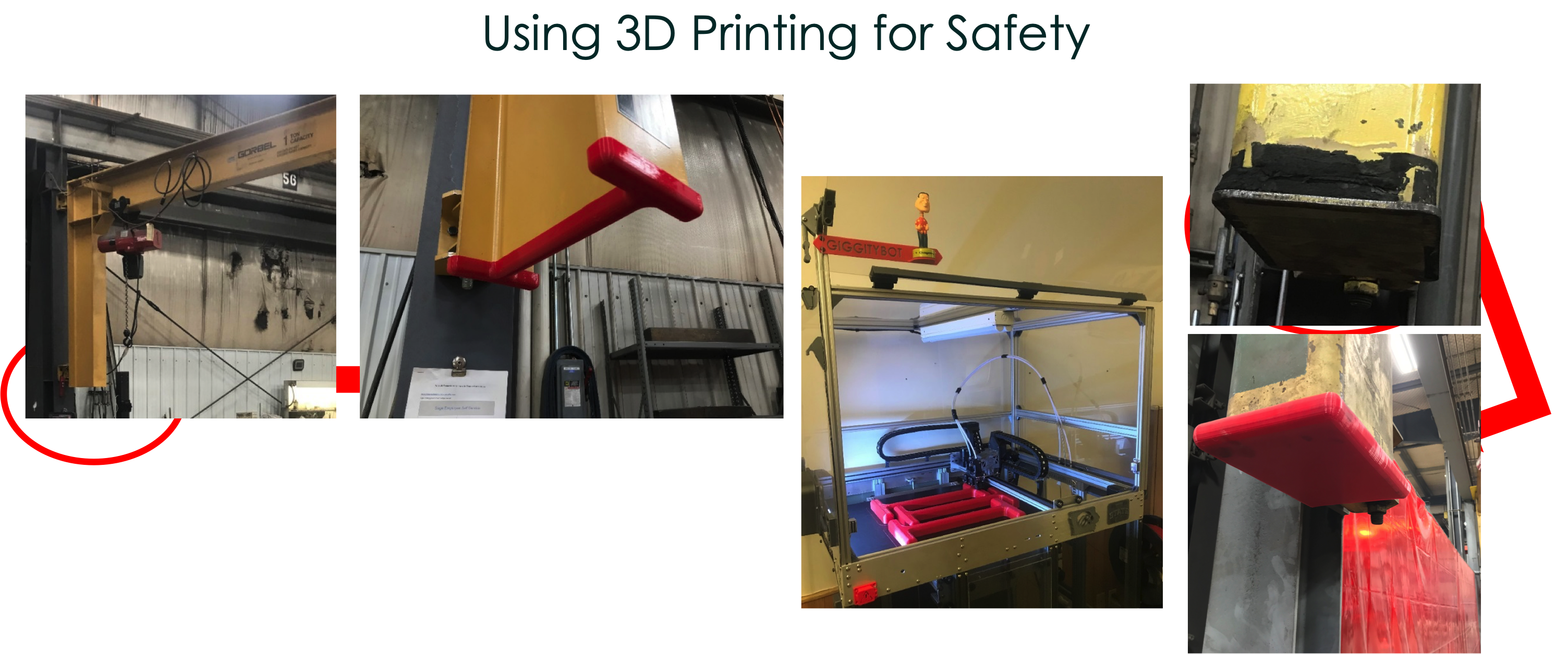
Using 3D Printing for Safety - 2018 brought new and exciting ideas to the Stellar manufacturing floor and the world of safety. With the purchase of two 3D printers. We quickly found ways to ensure personal protection adding soft plastic to areas eliminating blunt or sharp edges throughout the shop floor. These are just a couple of examples of making a safer place to work.
John Deere Dubuque Works - Dubuque, IA
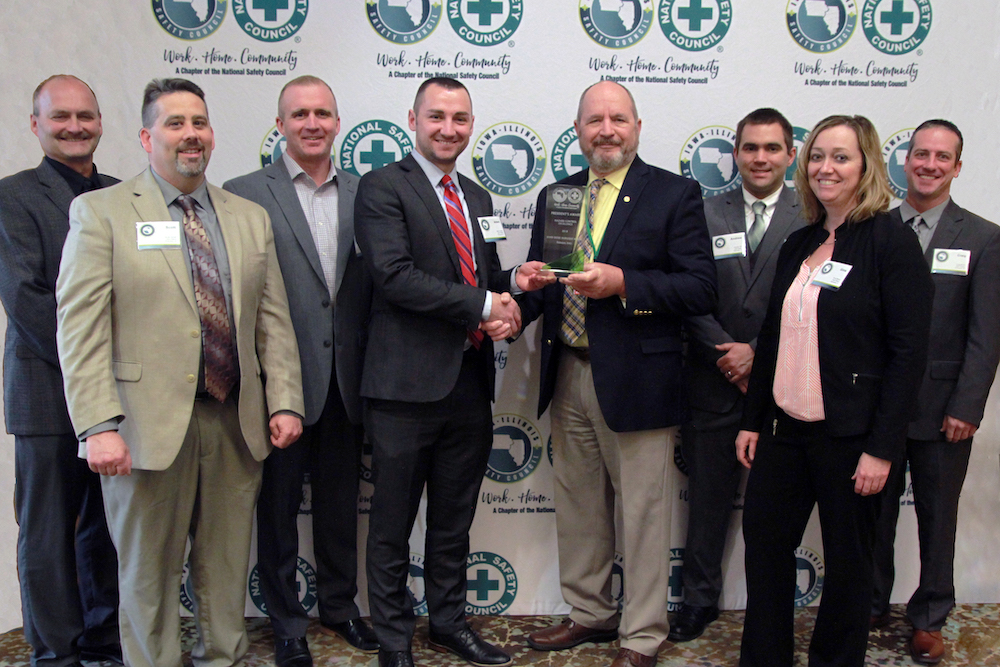
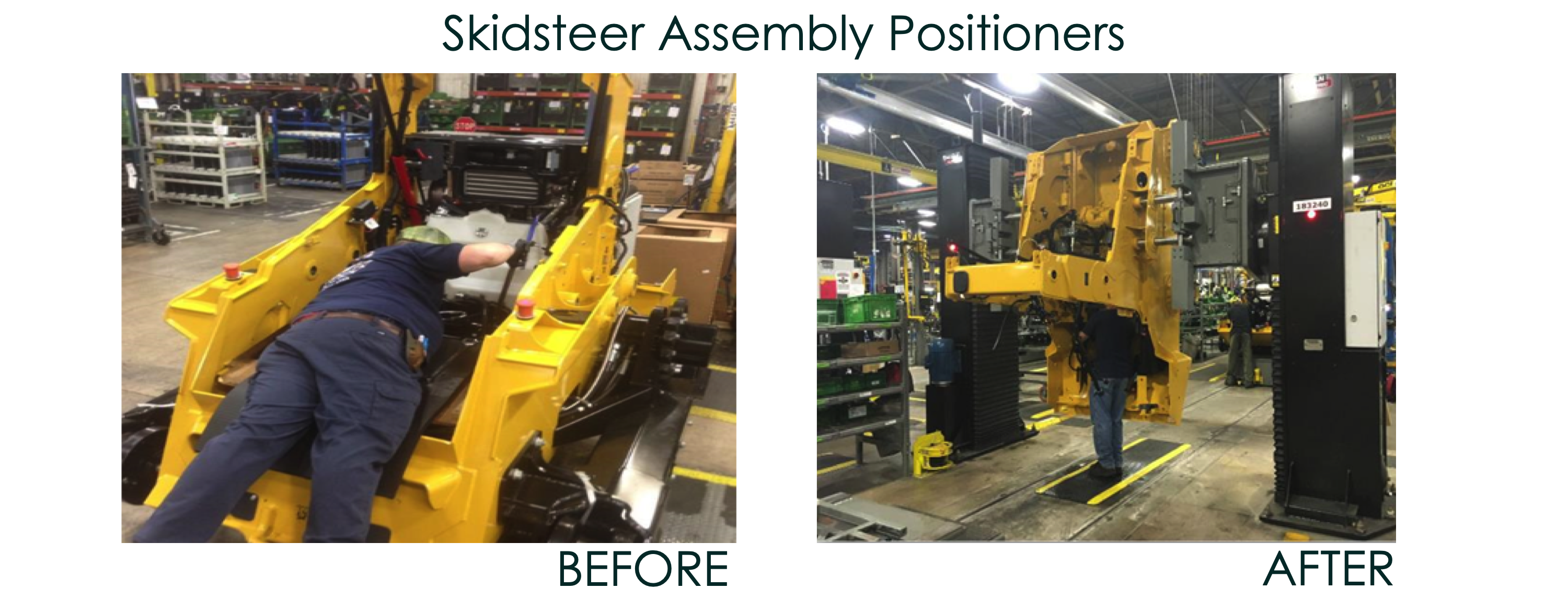
Skidsteer Assembly Positioner
Before: As a result of the Skidsteer design, many assemblers required to perform assembly tasks in awkward positions on the assembly line. This created many ergonomic concerns which has resulted in 19 safety incidents since 2012.
After: Custom fixtures, incorporated onto positioners, allows the frame to be rotated and positioned to a height that fits the work to the worker mitigating ergonomic risks. Since implementation in the Spring of 2018, there has been 0 safety incidents involved with work performed at these positioners.
Hawkeye Ready Mix - Cedar Rapids, IA
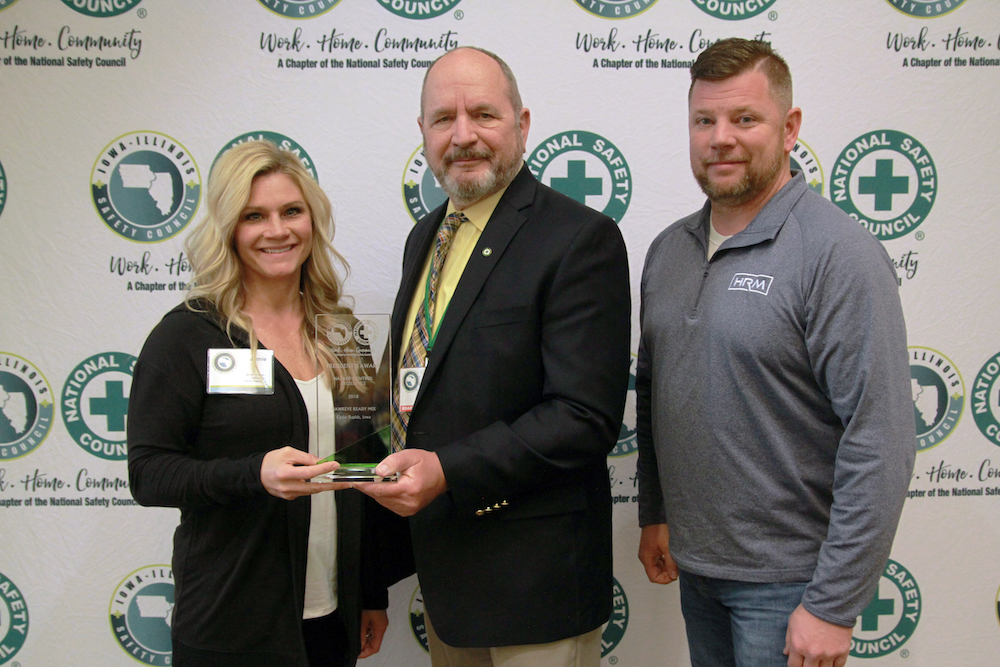
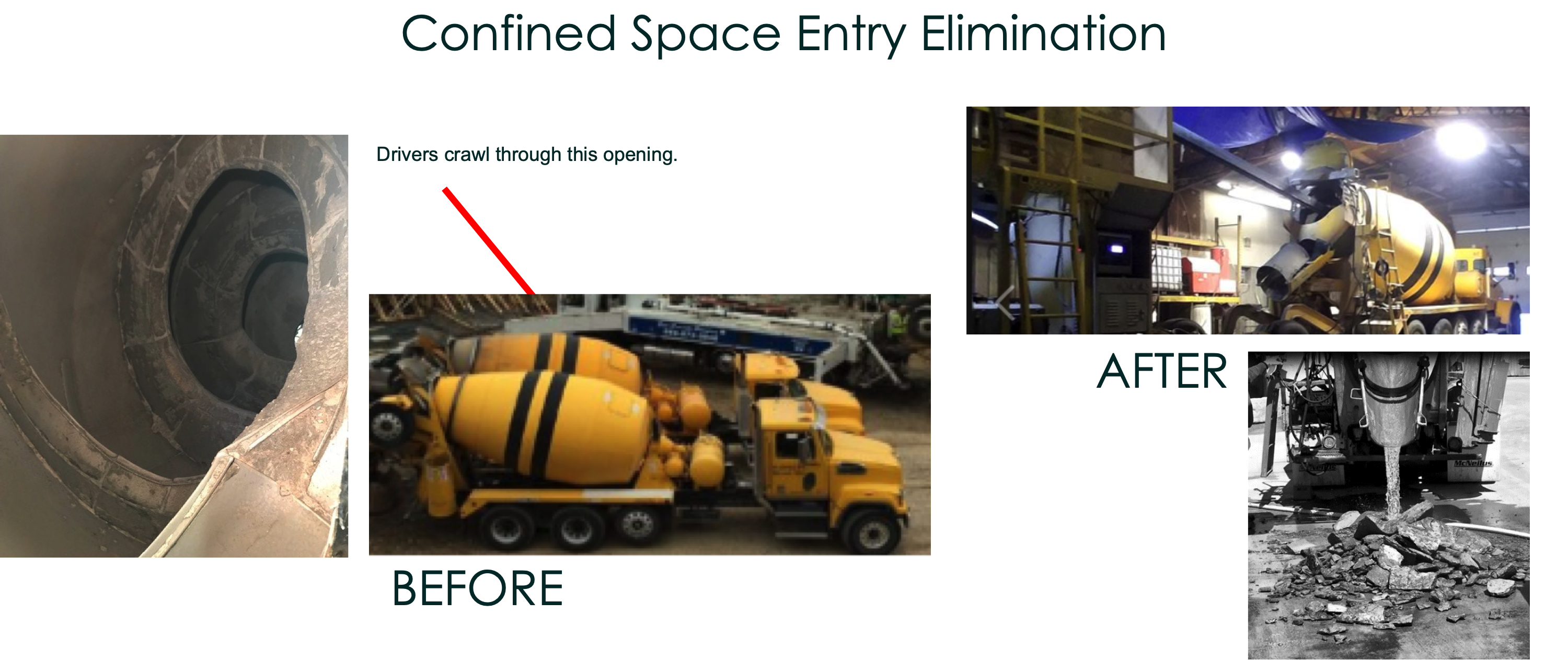
Confined Space Entry Elimination
Before: Ready Mix drivers were responsible for removing concrete build up on the inside of their drum, approximately once to twice a year. To remove concrete the driver enters through the small hatch on the side of the drum. This hole is extremely small. Once inside they are exposed to the following:
1. Confined Space - Permit Required w/a spotter.
2. Hearing Conservation - use of vibrating air chisel requires double hearing protection.
3. Trip/Slip Hazards - the air chisel combined with water to reduce the silica dust, but creates a wet slippery uneven surface inside.
4. Respiratory Protection - Silica Dust requires employees to wear respiratory mask and enter into the Respiratory Protection Plan for Silica.
5. Falling Hazards - When chunks of hardened dead concrete break loose, could impact the employee. Hard Hats are required.
After: The company instituted new state-of-the-art technology called the Ready Jet, the first in Iowa. A 3rd party comes twice a year with the machine and cleans all drums. No employees have to enter the drums anymore for clean out. This technology uses a hydraulic action along with water pressure of 20,000 PSI to remove the concrete, which doesn't damage the drum. The arm enters through the hopper of the drum. When finished, the excess concrete is dumped out the chute. We have successfully removed around 50 employees from the hazards above!
Full size photos of the President's Award Recipients and all Hazard Control Recognition submissions can be viewed in the Hazard Control Recognition library in the "Members Only" section.
All awards photos can be viewed and downloaded at the
Photos page.